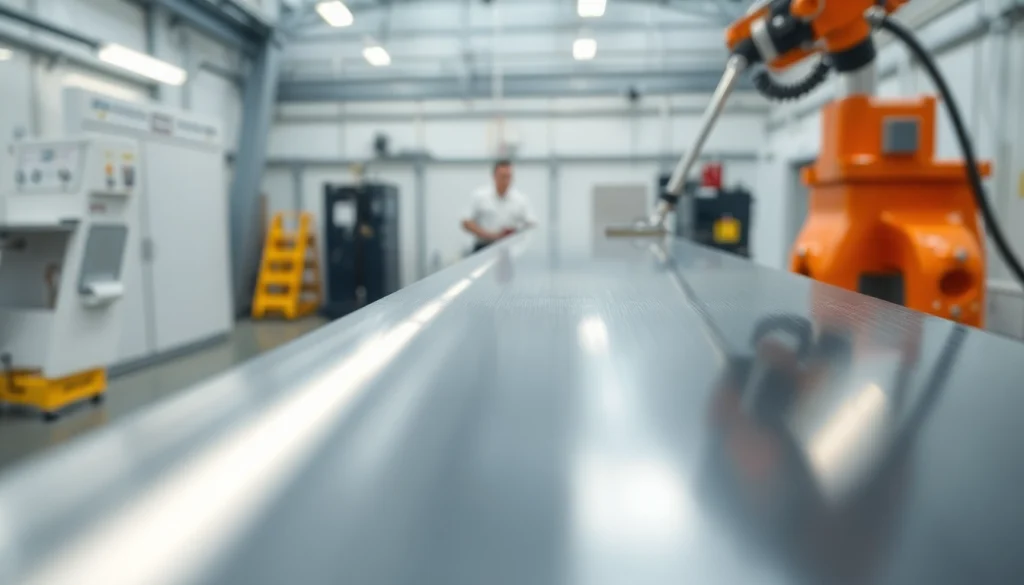
Understanding EP Coating: Basics and Benefits
What is EP Coating?
Electrophoretic coating, commonly referred to as ep coating, is a versatile surface coating technology that utilizes electric charge to deposit paint onto surfaces, particularly metals. The process involves immersing the parts to be coated in a liquid paint bath while applying an electrical current, which causes the paint to migrate toward and adhere to the conductive surfaces. This technique is recognized for creating an even and uniform coating that effectively protects against corrosion, wear, and oxidation, making it especially valuable in industries where durability and resilience are paramount.
Key Benefits of Using EP Coating
- Superior Corrosion Resistance: EP coating offers exceptional resistance to rust and other forms of corrosion, significantly extending the lifespan of coated products.
- Uniform Coverage: The process ensures an even application, eliminating uncoated spots and providing full surface coverage—even in hard-to-reach areas.
- Environmental Friendliness: Many EP coatings are water-based, making them more environmentally friendly than traditional solvent-based paints.
- Versatility: Applicable across a range of metals, EP coating is ideal for various products from automotive components to household fixtures.
- Cost-Effectiveness: By minimizing waste and improving durability, EP coating processes can lead to significant cost savings over time.
Industries That Utilize EP Coating
Electrophoretic coating finds applications across multiple sectors. Some notable industries include:
- Automotive: Used widely to coat car parts for enhanced corrosion resistance.
- Aerospace: Essential for protecting aircraft components from environmental damage.
- Electronics: Provides critical protection against elements that could affect performance.
- Consumer Goods: Commonly used for household items, improving both functionality and aesthetics.
- Industrial Equipment: Coating tools and machinery to extend service life and reduce maintenance costs.
EP Coating Process: Step-by-Step Guide
Preparation of Surfaces for EP Coating
Successful electrophoretic coating begins with proper surface preparation, which includes cleaning, degreasing, and etching surfaces to enhance coating adhesion. The steps include:
- Cleaning: Remove contaminants like grease and dirt using appropriate cleaning agents.
- Degreasing: Follow up with degreasers to eliminate any oil residues.
- Etching: Utilize acids to create a micro-textured surface, enhancing the bond between the coating and the substrate.
Application Techniques for Optimal Results
Once prepared, the application process can begin. This stage typically involves:
- Immersion: The metal parts are submerged in the paint bath containing charged paint particles.
- Electrophoretic Deposition: Upon application of an electric current, particles migrate toward the substrate, forming a uniform layer.
- Separation: The workpiece is withdrawn from the tank, and excess paint is allowed to drain.
Curing and Finishing Touches in EP Coating
Finally, curing solidifies the coating, enhancing its durability and resistance:
- Curing Stage: The coated items are subjected to heat, enabling the paint to properly set and adhere to the surface.
- Final Inspection: Each coated product is inspected for quality, checking for any defects or inconsistencies.
Comparative Analysis: EP Coating vs Other Coating Methods
EP Coating vs Powder Coating
When comparing EP coating to powder coating, various factors come into play:
- Application Method: While EP coating uses an electric current to adhere paint onto surfaces, powder coating relies on an electrostatic charge followed by heat curing.
- Thermal Resistance: Powder coating is generally more resistant to higher temperatures compared to EP coating, making it suitable for applications subject to extreme conditions.
- Environment : EP coatings are often more solvent-friendly, utilizing water-based solutions versus the chemical solvents used in powder types.
- Finish Aesthetic: Powder coatings tend to offer a thicker finish with a textured appearance, whereas EP coatings have a smoother, more uniform surface.
When to Choose EP Coating Over Traditional Methods
Choosing EP coating may be preferable under certain conditions:
- When the application requires maximum corrosion resistance.
- If you need to coat complex geometries or difficult-to-reach surfaces.
- When seeking an environmentally friendly solution.
- In applications requiring a thin and even coating.
Case Studies: Successful EP Coating Implementations
Several companies have successfully implemented EP coating, resulting in improved product performance:
- Automotive Applications: A leading automotive manufacturer utilized EP coating to enhance the durability of their vehicle exteriors, leading to significant improvements in customer satisfaction regarding rust and corrosion issues.
- Industrial Machinery: An industrial equipment producer employed EP coating on components exposed to harsh environments, resulting in reduced operational failures and maintenance downtime.
Challenges and Solutions in EP Coating
Common Issues Faced During Application
Despite its advantages, there are challenges associated with EP coating:
- Inconsistent Coating: Variations in electric current or bath temperature can lead to uneven coatings.
- Surface Contamination: Any residues left on substrates can impact adhesion, leading to defects.
Troubleshooting EP Coating Problems
Addressing issues effectively often involves:
- Regular Monitoring: Continuously check electrical parameters and adjust as necessary.
- Enhancing Cleaning Protocols: Maintain stringent cleaning processes to avoid contamination.
Best Practices for Maintaining Quality Coatings
To ensure high-quality outcomes, manufacturers should follow these best practices:
- Routine Equipment Calibration: Regularly calibrate deposition equipment to maintain optimal performance.
- Invest in Training: Provide workers with ongoing training to understand the nuances of the EP coating process.
Future Trends in EP Coating Technology
Innovations Impacting EP Coating Processes
Emerging technologies are continuously enhancing EP coating processes, including:
- Smart Coatings: Development of smart coatings that can respond to environmental stimuli to provide additional protection.
- Nano-Coatings: These next-generation coatings could offer enhanced properties, such as self-cleaning capabilities and improved scratch resistance.
Sustainability in EP Coating Practices
With increasing awareness of environmental impacts, EP coating practices are moving toward sustainability:
- Water-Based Solutions: A growing shift towards less harmful, water-based materials is being embraced.
- Waste Reduction: Innovative recycling techniques for overspray and waste materials are being implemented, maximizing material usage.
The Future of EP Coating in Various Industries
As industries evolve, the application of EP coating is set to expand, especially in sectors like renewable energy, where protective coatings are crucial for the longevity of products exposed to the elements. Predicting its future scope, EP coating may become a standard in enhancing sustainability across manufacturing processes.