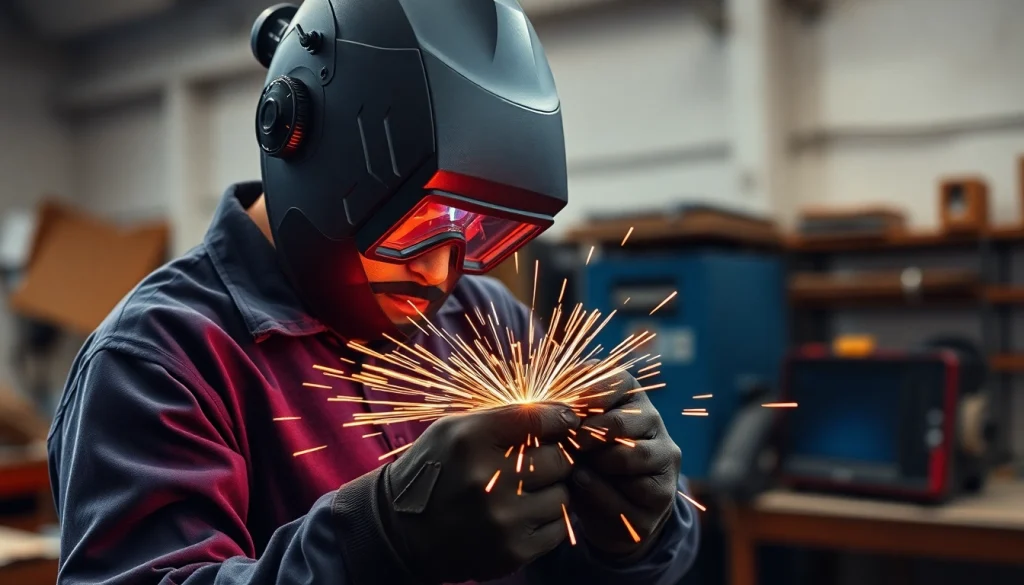
Understanding the Unimig TIG Welder
What is a TIG Welder?
TIG welding, or Tungsten Inert Gas welding, is a sophisticated welding process highly favored for its precision and control. It employs a non-consumable tungsten electrode to produce the weld, which is protected by an inert gas, usually argon. This method is ideal for welding thin sections of metal, giving welders the ability to make clean, strong joints across a variety of materials, including stainless steel, aluminum, and copper.
Benefits of Using a Unimig TIG Welder
Unimig TIG welders are engineered to cater to both amateur and professional welders, offering numerous advantages that enhance the welding experience:
- Precision: The ability to control heat and the speed of the welding process allows for intricate designs and clean joints.
- Versatility: Unimig TIG welders can handle a wide array of materials, including dissimilar metals, making them ideal for automotive, aerospace, and manufacturing applications.
- Clean Process: The use of inert gas minimizes spatter and oxidation, leading to tidy results without the need for extensive cleanup.
- Powerful Performance: Unimig welders are known for their robust design, providing reliable performance even in industrial settings.
Basic Components of a Unimig TIG Welder
A typical Unimig TIG welder consists of several key components that work together to facilitate the welding process:
- Tungsten Electrode: The core element that conducts the current and provides the arc for welding.
- Gas Lens: A device that helps control the flow of shielding gas, ensuring a consistent and clean weld.
- Foot Pedal: Allows the welder to control the amperage during the welding process, providing increased versatility.
- Cooling System: Essential for maintaining optimal temperatures, preventing overheating, and ensuring a longer lifespan of the welder.
Key Features of Unimig TIG Welders
Power Options: AC and DC Explained
One of the foremost features of Unimig TIG welders is their power options, which can be either AC (Alternating Current) or DC (Direct Current).
AC is generally used for welding aluminum and magnesium, providing clean and strong welds by alternating the direction of the current. DC, on the other hand, is favored for welding ferrous metals such as steel and stainless steel. This flexibility allows users to tackle various welding projects efficiently.
Control Settings and Their Importance
An essential feature of Unimig TIG welders is their control settings, which significantly influence the quality of welding. These controls may include:
- Amperage Control: Adjusting the current helps in managing the heat input and penetration based on the material.
- Post-Flow Control: This setting ensures that the shielding gas continues to flow after the arc is extinguished, preventing oxidation on the weld.
- Pulse Settings: Allow for easier welding of thin materials and reduce distortion through controlled heat application.
Portability and Design Considerations
Unimig welders come in various designs, from lightweight models for portable use to durable, heavy-duty units suited for industrial environments. Portability is an essential factor for many welders, as it allows flexibility in job locations—from workshops to on-site projects.
Ergonomic designs and compact forms are standard in Unimig products, making them easy to handle, transport, and store without compromising performance.
Popular Unimig TIG Welder Models
Overview of the Viper Series
The Unimig Viper series is designed for versatility, catering to a range of welding requirements from hobbyists to serious professionals. Models like the Viper TIG 180 AC/DC Mk II come equipped with advanced features such as high-frequency start, adjustable pulse settings, and a user-friendly interface, allowing for precise settings tailored to various welding tasks.
Exploring the Razor Series
The Razor series represents the top-tier offerings from Unimig, aimed at high-performance needs. The Razor TIG 200 AC/DC model excels in professional and industrial sectors, providing unmatched reliability, superior technology, and consistent results. With enhanced duty cycle ratings and sophisticated control panels, these models handle demanding environments with ease.
Comparative Analysis of Unimig Models
When comparing Unimig models, consider factors like:
- Power Output: Ranging from entry-level to high-output models, suitable for different applications.
- Control Features: Some models may offer more advanced controls, including dual settings for specialized projects.
- Weight and Portability: Depending on your working environment, heavier machines may provide better stability, while lighter models offer mobility.
Choosing the Best Unimig TIG Welder for Your Needs
Assessing Your Welding Projects
Before selecting a Unimig TIG welder, consider the types of welding projects you’ll be undertaking. For instance, if you’re working on thin materials or delicate designs, a model with precise amperage control and pulsing capability would be beneficial. Conversely, if your work involves heavier gauge materials, a more powerful model with a higher duty cycle would suit your needs.
Budget Considerations When Buying
Welders, including Unimig’s range, come at various price points. Setting a budget is critical not only for the welder itself but also for additional costs such as consumables and maintenance. Evaluate the long-term benefits of investing in a high-quality welder that may cost more upfront but will deliver better performance and durability over time.
Reviews and Customer Feedback
Before finalizing a purchase, it’s advantageous to read reviews and gather customer feedback. Many platforms provide insightful user experiences that can help you understand the strengths and potential shortcomings of various Unimig models, ensuring you make a well-informed decision.
Maintaining Your Unimig TIG Welder
Regular Maintenance Practices
Maintaining your Unimig TIG welder is essential for preserving its functionality and longevity. Regular maintenance practices include:
- Cleaning: Keep the welder and accessories clean from dirt and debris. Regularly check and replace the tungsten electrode as needed.
- Inspecting Connections: Ensure all cables and connections are secure and free of frays that could affect performance.
- Cooling System Maintenance: Check coolant levels and ensure the system is functioning effectively to prevent overheating.
Troubleshooting Common Issues
Even with proper maintenance, problems can arise. Common issues include:
- Inconsistent Arc: This can often be traced back to the tungsten electrode or improper settings. Ensure proper electrode length and clean connections.
- Excessive Spatter: Typically a sign of incorrect settings or improper gas flow. Adjust the gas flowrate or check for leaks in hoses.
Resources for Further Instruction
For users looking to deepen their knowledge, many resources are available, including instructional videos, user manuals, and community forums where experienced users share tips and troubleshooting advice. Exploration of these resources can significantly enhance your welding skills.