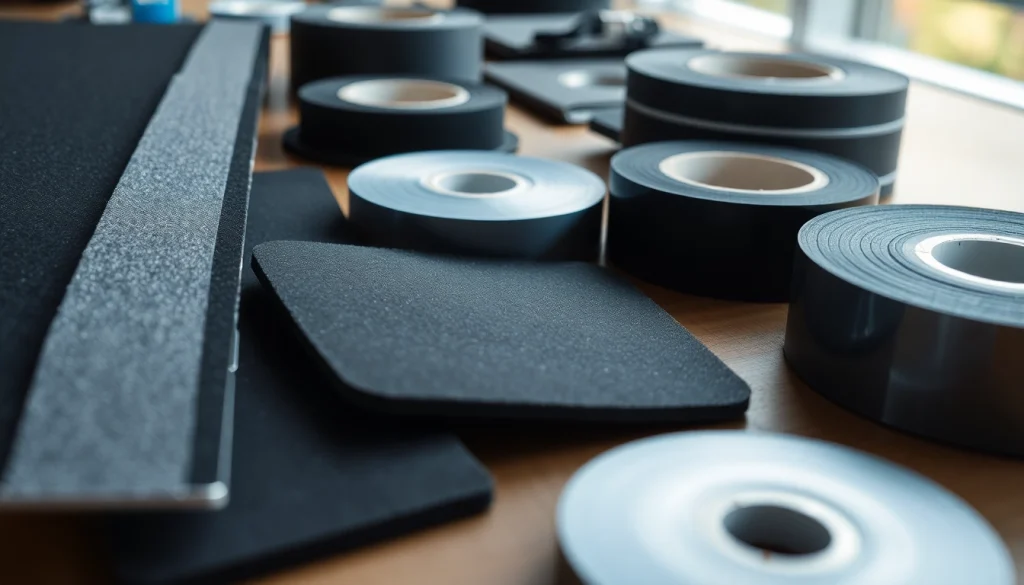
Understanding Thermal Management Materials
In the rapidly advancing world of electronics, effective thermal management is crucial to ensure optimal performance and longevity of devices. Thermal management materials play a vital role in dissipating heat generated by electronic components, thus protecting them from heat-related failures. This comprehensive guide delves into the nature of these materials, their applications, innovations, and performance metrics, enabling manufacturers and engineers to make informed decisions in their thermal design processes.
What Are Thermal Management Materials?
Thermal management materials encompass various products designed to control, transfer, and dissipate heat in electronic applications. These materials aim to reduce thermal resistance between heat-generating components and heat sinks, ensuring that the operational temperature of devices remains within safe limits. The effectiveness of thermal management strategies can significantly influence the performance, reliability, and energy efficiency of electronic systems.
Types of Thermal Management Materials
Several types of thermal management materials are available, each with unique properties tailored for different applications. The main categories include:
- Thermal Interface Materials (TIMs): These materials are used to fill microscopic gaps between surfaces to enhance thermal conduction. Common types include thermal pastes, gels, and phase change materials.
- Gap Fillers: Typically soft, conformable materials, gap fillers help bridge spaces in assemblies and reduce thermal resistance. They are used in high-performance applications where heat dissipation is crucial.
- Thermal Pads: These are pre-formed pads that provide effective thermal conductivity while eliminating the need for messy thermal pastes. They are commonly made from silicone, polymer, or other compounds.
- Thermal Adhesives: These not only provide thermal management but also bond components together. Their dual function can save weight and space in compact electronic devices.
- Heat Spreaders: Made from metals like copper or aluminum, heat spreaders distribute heat across a larger area, preventing hotspots in high-performance applications.
- Phase Change Materials (PCMs): These materials absorb excess heat during operation and release it when the temperature drops, helping maintain a stable temperature environment.
How Thermal Management Materials Work
The primary function of thermal management materials is to facilitate heat transfer away from components generating excess heat. This process involves three mechanisms: conduction, convection, and radiation:
- Conduction: This is the most critical mechanism in TIMs and gap fillers, which conduct heat away from hot surfaces and into heat sinks or spreaders.
- Convection: This process occurs in systems exposed to air or liquids, where heat is transported away by the movement of air or coolant.
- Radiation: Though less common in electronic applications, radiant heat transfer occurs through electromagnetic waves and is critical in some specific thermal management scenarios.
Key Applications of Thermal Management Materials
Use Cases in Electronics
Thermal management materials are ubiquitous in various electronic applications, ranging from consumer electronics to high-end computing and industrial equipment. Here are some notable use cases:
- Consumer Electronics: Smartphones, tablets, and laptops generate significant heat during operation. Here, effective heat dissipation extends device lifespan and enhances performance.
- Automotive Electronics: Modern vehicles rely heavily on electronics, from navigation systems to engine management. High-quality thermal management materials ensure these systems operate reliably under varying temperature conditions.
- Telecommunications: Telecom equipment, such as data centers, need efficient thermal management due to their high-density layouts and power consumption.
- Industrial and Military Equipment: Tough environments demand reliable thermal solutions to prevent failures that could lead to operational risks.
Impact on Product Performance
Effective thermal management directly influences product performance and reliability. With proper materials in place, electrical components can run at optimal temperatures, resulting in:
- Increased Efficiency: Lower operational temperatures allow devices to function within their design specifications.
- Extended Lifespan: Heat is a major contributor to component failure; by managing it effectively, the longevity of electronic devices significantly improves.
- Improved Reliability: Devices are less likely to experience heat-related failures, making them more dependable in critical applications.
- Enhanced Performance: Improved heat dissipation can lead to better efficiency in power consumption and processing capabilities.
Case Studies
Numerous case studies highlight the crucial role of thermal management materials in enhancing electronic performance:
- Case Study 1 – Consumer Electronics: A leading smartphone manufacturer incorporated advanced thermal interface materials in their latest model, leading to a 15% improvement in battery efficiency and a reduction in thermal throttling incidents.
- Case Study 2 – Automotive Sector: An electric vehicle company utilized specific gap fillers and thermal pads to manage heat in their battery packs, resulting in a 20% increase in driving range due to better thermal efficiency.
- Case Study 3 – Data Centers: A telecommunications provider implemented phase change materials in high-density server arrangements, resulting in a marked decrease in cooling costs and improved server uptime.
Selecting the Right Thermal Management Materials
Factors to Consider When Choosing Materials
Selecting the right thermal management material for a specific application requires careful consideration of several factors:
- Thermal Conductivity: Evaluate the material’s ability to conduct heat, measured in Watts per meter Kelvin (W/mK). Higher values indicate better performance.
- Mechanical Properties: Consider the stiffness, adhesion, and compression resistance necessary for the intended application.
- Operating Temperature Range: Ensure the material can withstand the temperatures it will encounter during operation.
- Application Environment: Assess whether the environment is clean, dusty, or exposed to chemicals, as this will impact material choice.
- Cost Considerations: Evaluate the budget without compromising performance. Sometimes, a slightly more expensive material can result in substantial long-term savings through improved efficiency.
Common Mistakes to Avoid
When selecting thermal management materials, several pitfalls can compromise both strategy and performance:
- Underestimating Thermal Resistance: Choosing materials without considering thermal resistance can lead to overheating and device malfunction.
- Neglecting Application Requirements: Failing to account for environmental conditions such as humidity can lead to material degradation over time.
- Ignoring Manufacturer Specifications: Skipping specifications can result in using materials outside their operational capacity, leading to failures.
- Not Considering Long-Term Effects: Focus on immediate performance without weighing long-term effects can lead to recurrent issues.
Expert Recommendations
To navigate the complexities of selecting thermal management materials, consult with specialists who can provide insights tailored to specific applications. Also:
- Perform comparative testing of materials to verify claims of thermal performance.
- Use modeling software for simulations to predict thermal performance before material implementation.
- Consider customized solutions that can specifically address application needs, particularly in high-performance or critical environments.
Innovations in Thermal Management Technologies
Emerging Trends
As technology evolves, so do thermal management solutions. Notable trends include:
- Advanced Materials: Development of graphene and carbon nanotube composites represents cutting-edge advancements that could revolutionize thermal management due to their exceptional thermal conductivity.
- Smart Materials: Growing interest in phase change materials that can react to temperature changes offers dynamic heat management solutions, particularly in environments with fluctuating conditions.
- Integration of IoT: The advent of IoT sensors enables real-time monitoring of thermal conditions, allowing for responsive adjustments in cooling systems.
Future of Thermal Management Materials
The future of thermal management materials is promising, driven by the continuous push for higher efficiency, miniaturization of components, and the ever-increasing demand for performance. Anti-reflective coatings and advanced manufacturing techniques are likely to play key roles in creating materials that can sustain the highs of modern electronics.
Impact on Sustainability
With rising environmental awareness, sustainable practices are becoming integral in the selection and development of thermal management materials. Innovations aimed at recyclable materials, bio-based options, and reduction in manufacturing waste are indicative of a shift towards environmentally-friendly solutions. Pressure from regulatory standards will likely amplify focus on sustainability within the thermal management sector.
Measuring Performance of Thermal Management Materials
Key Performance Indicators
To assess the effectiveness of thermal management materials, several critical performance indicators are considered:
- Thermal Conductivity: Measurement is key to identifying how well a material transfers heat.
- Thermal Impedance: This metric helps evaluate how much resistance a material poses to heat flow, measured generally in °C/W.
- Durability and Life Cycle: Assessment of material longevity and performance consistency over time and under different environments.
- Ease of Application: Consideration of how straightforward the installation process is, which can affect overall efficiency and costs.
Testing Methods
Multiple testing methods can provide reliable data on thermal management material performance:
- Guarded Hot Plate Method: A standard approach for measuring thermal conductivity under steady-state conditions.
- Laser Flash Analysis: This method measures thermal conductivity over short distances and assesses how quickly a material can conduct heat.
- Thermal Imaging: Utilizing infrared cameras to visualize heat flow in devices can help identify areas of thermal inefficiency.
Evaluating Material Effectiveness
Ultimately, evaluating material effectiveness requires a holistic perspective that considers both quantitative data from tests and qualitative feedback from end-users regarding product performance and reliability. An iterative approach that combines empirical testing with practical use will lead to the optimization of thermal management solutions in real-world applications.